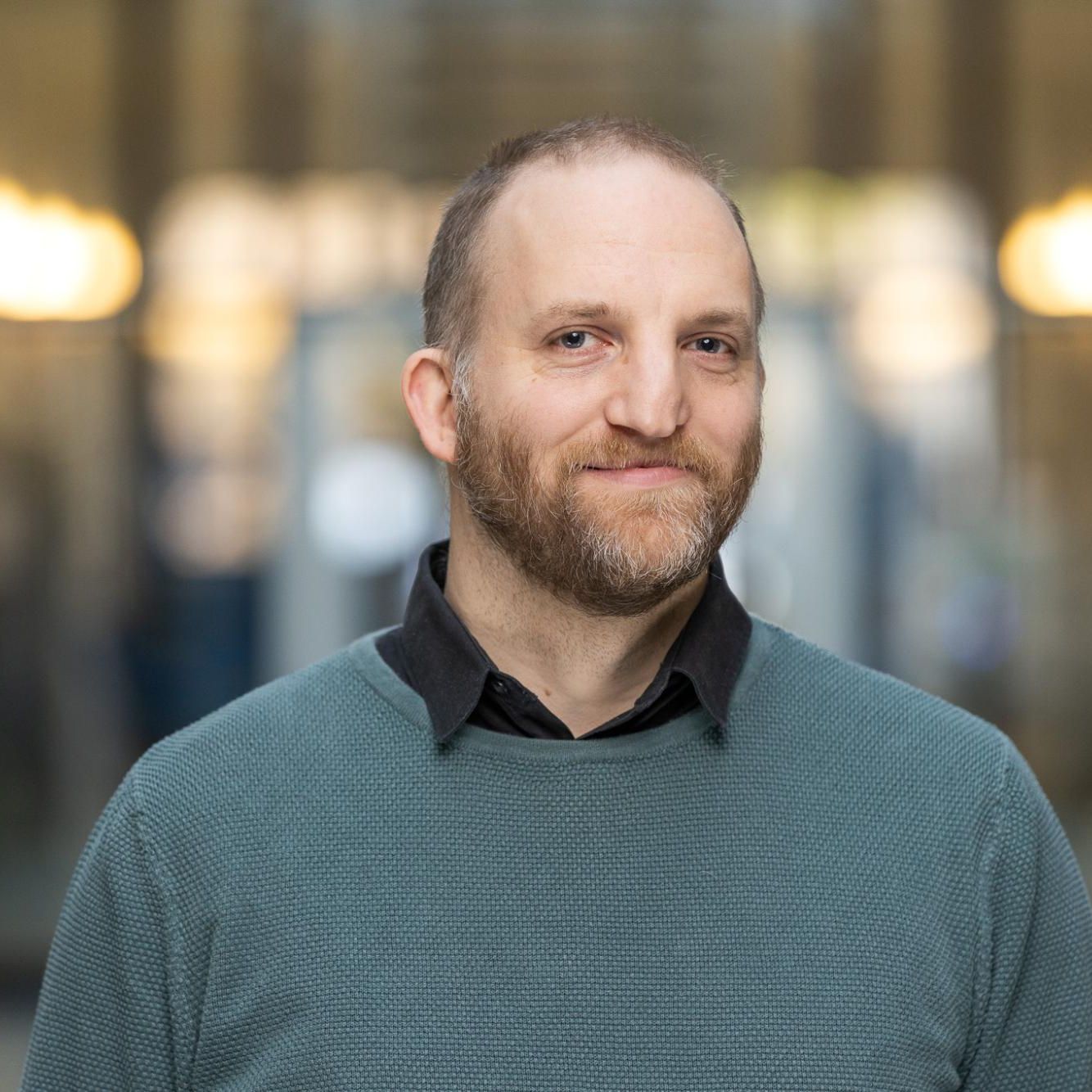.jpg)
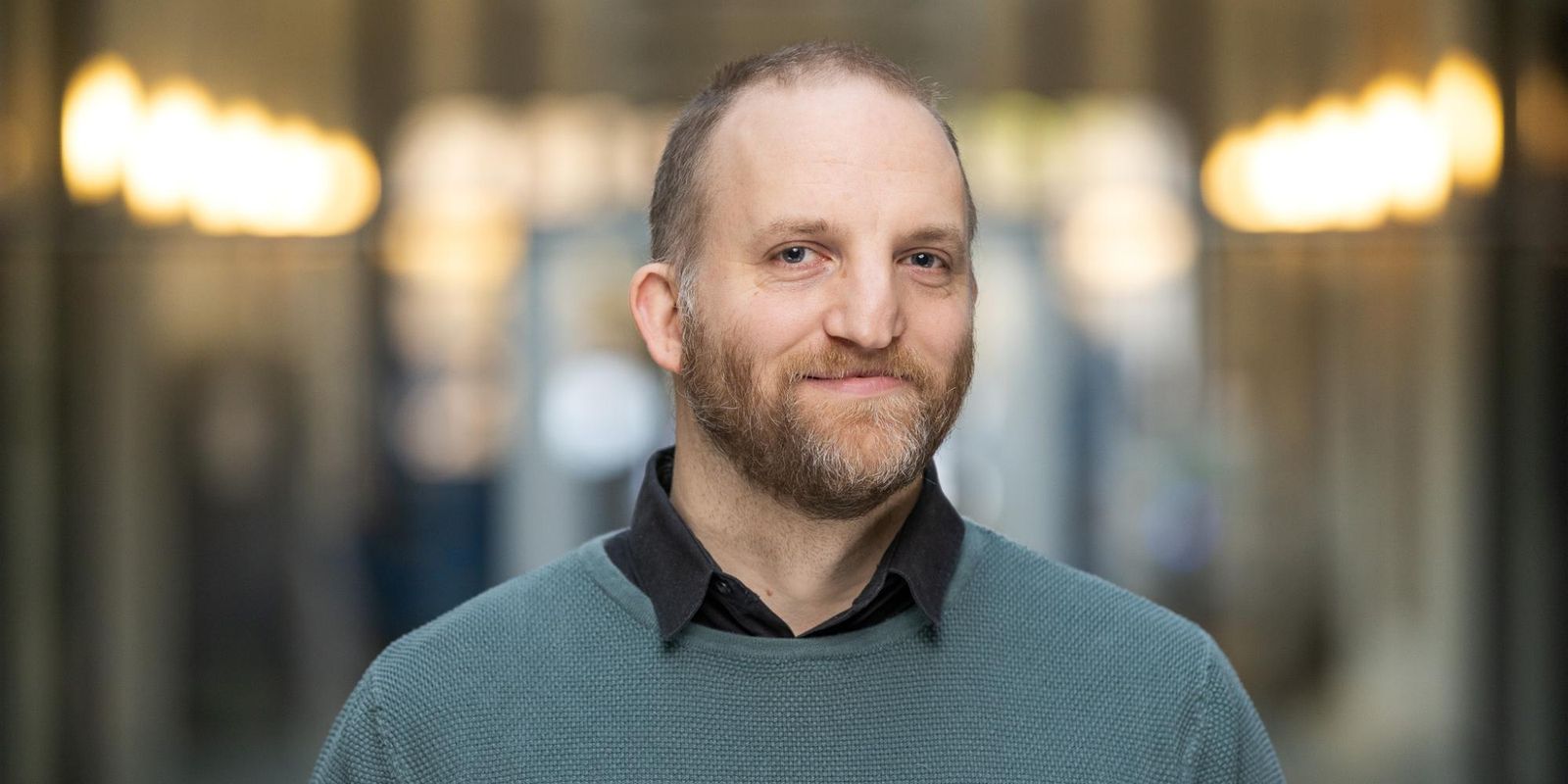.jpg)
"One of the first AI projects to be certified under EU standards."
Mechatronic system engineer Bas Vet
Read moreSystem engineer Ruud Hesselink is a mechanical engineer by trade, but today focuses on a system’s entire design. This is exactly what he did for the famous Polaroid instant photo camera, among others. In 2008, this company relaunched the plant in Enschede for the manufacture of film cartridges. Polaroid referred to this as ‘The Impossible Project’.
‘All of the knowledge was gone, and the chemical formulation and films, among other things, had to be redeveloped. It also was uncertain as to whether the old, extremely fast production lines that had long been dormant could be started back up again. The original film production machines still date from the fifties and are now being used again. We developed a new, robust module for cutting and laminating the films. That module had to fit into the old production line and at the same time had to be ready to accommodate new technologies and comply with current safety guidelines. The module had to have a long service life and had to be able to accommodate the high production rate of approximately 180 films per minute. In addition, the module had to be able to process a wide range of materials for multiple types of films and different camera models, in terms of type, thickness and width.’
‘Especially the machine’s high speeds were very challenging. The entire process must be executed within 330 milliseconds, perfectly timed with the old machine. This involves supplying the film, laminating, cutting and conveying it. Furthermore, the film is extremely thin and has a tendency to crumple. Everything must take place at the same position, at high speed, while taking the shape, precision, timing and film handling into account. How do you ensure that everything is in order at the right moment? Moreover, the machine had to be as low-maintenance as possible, because during maintenance it has to be shut down, of course. This meant that we also had to give careful thought to the machine’s parts.’
Together with the client we conducted a system analysis and evaluated concepts for the three main components: cutting and laminating the film, conveying the film and the photo materials. We evaluated these concepts in terms of proven technology, testability, reliability and any issues that could result in showstoppers. For the prototype we made use of leaf spring structures combined with a camshaft. As a result, each movement has its own servomotor and thus its own freedom relating to timing. Next, a virtual camming profile was developed with an encoder on the production line’s drive shaft. It is impossible to see this with the naked eye and we therefore used a high-speed camera to identify and adjust everything. It is gratifying to know that the “old-fashioned” Polaroid films now possess a touch of cutting-edge technology. I feel privileged to have been able to make a contribution to this achievement.’
Would you like to learn more about system engineering at Demcon? Come visit us for a cup of coffee (or tea). Send an email to coffee@demcon.com and we will be happy to contact you!
Mechatronic system engineer Bas Vet
Read moreAssembly operator 2 Gino Folkers
Read moreSenior mechanical engineer Michiel Aarts
Read moreSenior software engineer Pieter Bijleveld
Read more